Product / VDU
Halton Vita VDU – Decontamination unit
Halton Vita VDU is a 3-in-1 mobile hydrogen peroxide decontamination unit designed for efficiency, reliability, and effectiveness.
It ensures uniform distribution and complete decontamination of enclosed spaces of up to 750 m2 and hard-to-reach areas or surfaces with maximum safety. The unit is eco-friendly, reducing hydrogen peroxide to water and oxygen, leaving no harmful residues supporting sustainability goals. It has the potential to destroy the most resistant microbes, like bacterial spores, in low temperatures and low concentrations. It is dedicated to decontaminate demanding spaces such as industrial cleanrooms, laboratories, food production facilities, and healthcare spaces.
- Decontaminate large spaces efficiently due to high airflow with short process time.
- High user safety with remote operation and easily programmable.
- Material friendly, safe even for the most sensitive materials like electronics.
- Equipped with an integral sensor and facilitates up to four external sensors.
- Validated in a range of critical environments, proving its effectiveness and versatility.
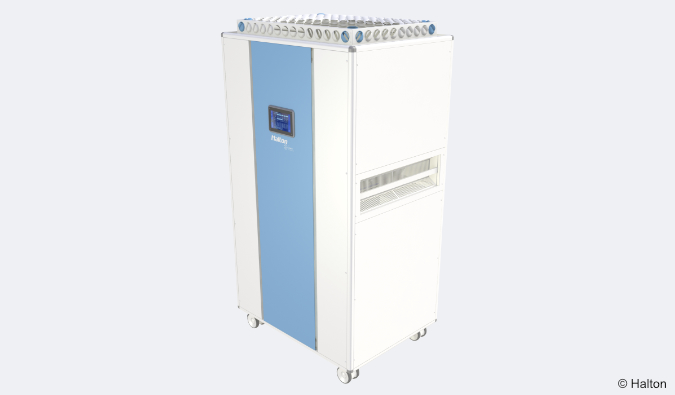
Overview
The Halton Vita VDU is a unique 3-in-1 mobile hydrogen peroxide (H2O2) decontamination unit that provides necessary air filtration, efficient vapour distribution and process verification. It has an integrated catalyser and is designed for demanding H2O2 bio-decontamination processes up to 750 m3 spaces. It uses up to 60% aqueous H2O2 solution to generate H2O2 vapours capable of destroying even the most resistant microorganisms, like bacterial spores, in room temperatures and low concentrations.
The process is carefully monitored and verified with integrated H2O2 sensor technology. The aeration process with an integrated catalyser removes residual H2O2 by decomposing into water and oxygen, leaving the space clean, safe, and ready for immediate use.
Application area
- Healthcare
- Pharma-, bio- and medical industry
- Food industry
- Univeristy and reserach laboratories
- Military sectors
Key features
- 3-in-1 system - vaporizing, vapour distribution and aeration.
- Allows the concentration to rise and then quickly return to working conditions.
- Decontaminate large spaces efficiently due to high airflow with short process time.
- High user safety with remote operation and easily programmable.
- Material friendly, safe even for the most sensitive materials like electronics.
- Equipped with an integral sensor and facilitates up to four external sensors.
- It offers the possibility for tailor-made integrations.
- Validated in a range of critical environments, proving its effectiveness and versatility.
Operating principle
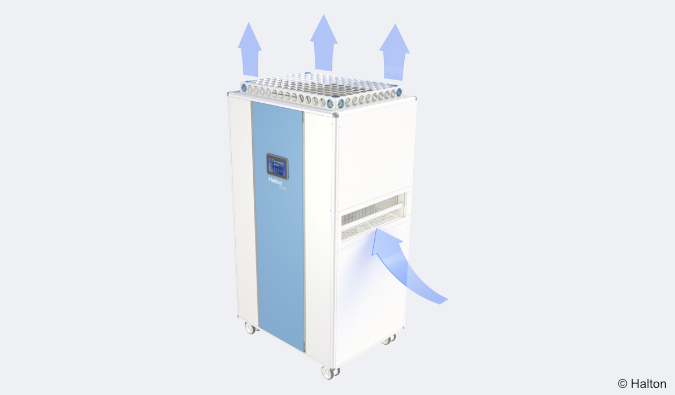
The Halton Vita VDU uses predefined decontamination programs for different types of areas. In the first stage of the process, filters draw air on both sides of the unit, and adjustable diffusers distribute vapourised hydrogen peroxide (vH2O2) from the top of the unit. It is equipped with an integral sensor and facilitates up to four external sensors, allowing verification of complete H2O2 distribution throughout the space. When the level of vH2O2 in the air reaches a certain level for a certain period, the air filtration phase takes place, and the filter cleans the drawn air inside the unit. The touch panel allows you to control the device remotely via the tablet.
The software inside the PLC (Programmable Logic Control) unit monitors data from the sensor(s). The sensor provides the following data from the enclosed space: hydrogen peroxide vapour ppm, temperature, humidity as relative saturation, relative humidity, dew point, and vapour pressure. Based on the data, the PLC controls the heating, blowing, and dosing of hydrogen peroxide to the vaporising units.
Key technical data
Feature | Description |
---|---|
Dimensions | 998 mm x 768 mm x 1895 mm (L x W x H) |
Weight | approx. 260 kg |
Airflow | 700 dm3/s / 2500 m3/h |
Filters | 300x750x38 mm, ePM1 55% 300x750x38 mm, ePM1 55% (Potassium permanganate) |
Features and options
Feature | Description |
---|---|
Color | Signal white + (antibacterial, RAL 9003, 30%) + blue (RGB 36-157-213) |
Casing | Galvanized steel / aluminium, White antibacterial epoxy polyester powder paint (RAL 9003, 30%) |
Connections | Power cord RS 485 / Max 4 sensors (vH2O2 ppm concentration, t, Rh, Rs) |
Compatible H2O2 solution | 35 - 60% hydrogen peroxide aqueous solution suitable for hydrogen peroxide vapour device, PT2 classification or higher |
Hydrogen peroxide output | 8,625 l/min at rate of 15 ml/min of H2O2 solution |
Power supply | 230 VAC/50Hz |
Fuses | F4 primary fuse (16A) |
F3 heat cell 5A | |
F2 power source 230V 3A | |
F1 power source 24V 3A | |
Control | 7" touch screen and computer / tablet / phone via cable or WiFi. Hydrogen peroxide |
Structure and materials
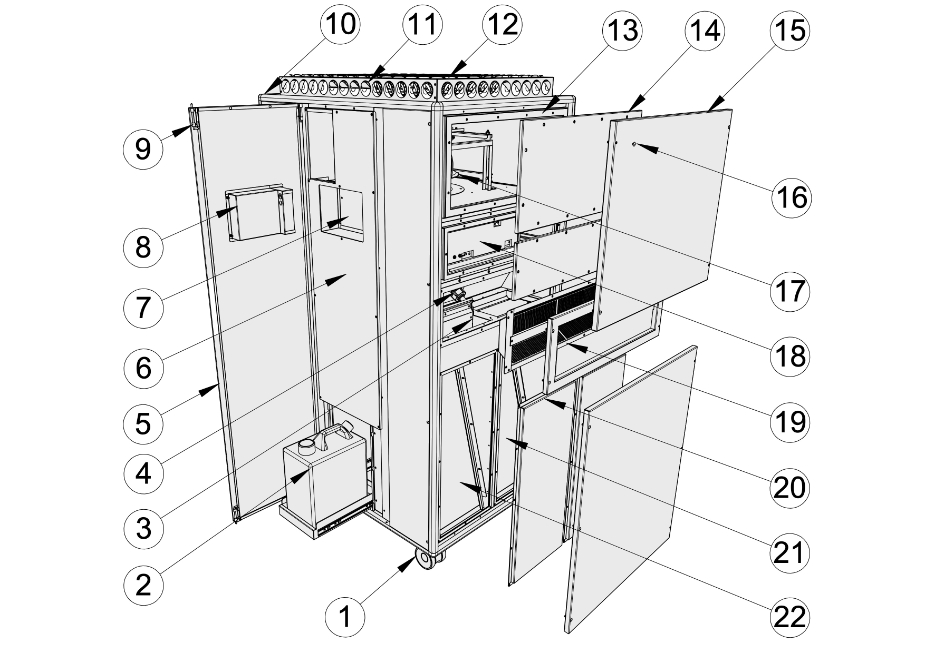
No. | Part | Material | Note |
---|---|---|---|
1 | Wheel | Plastic wheel with steel bearings | Two wheels are lockable. Tenet 5947UAP100P30-11_RAL9002 |
2 | Peroxide tank | Plastic | Tank capasity 10 l |
3 | Blade damper | Steel with antimicrobial epoxy-polyester powder paint finishing, white (RAL 9003/30%) | - |
4 | H2O2, humidity and temperature sensor probes | - | - |
5 | Service door | Galvannealed steel with epoxy-polyester powder paint finishing, blue (RGB 36-157-213) | - |
6 | Electrical cabinet service door | Galvannealed steel with antimicrobial epoxy-polyester powder paint finishing, white (RAL 9003/30%) | - |
7 | Electrical cabinet assembly | Galvannealed steel with antimicrobial epoxy-polyester powder paint finishing, white (RAL 9003/30%) | - |
8 | Touch screen display box | Galvannealed steel with antimicrobial epoxy-polyester powder paint finishing, white (RAL 9003/30%) | - |
9 | Service door hidge | Acid proof steel | - |
10 | Frame profile | Aluminium profile with antimicrobial epoxy-polyester powder paint finishing, white (RAL 9003/30%) | - |
11 | Nozzle | Plastic (Polyacetal (POM)) | Colour alternatives: White, black, grey and blue |
12 | Top nozzle hat box | Steel with antimicrobial epoxy-polyester powder paint finishing, white (RAL 9003/30%) | - |
13 | Service door gasket | Cellular polyethylene foam | - |
14 | Inner service doors | Aluminium with antimicrobial epoxy-polyester powder paint finishing, white (RAL 9003/30%) | - |
15 | Cover plates | Aluminium with antimicrobial epoxy-polyester powder paint finishing, white (RAL 9003/30%) | - |
16 | Cover plate opening hole plug | - | - |
17 | Fan | - | - |
18 | Evaporator assembly | - | - |
19 | Air intake grille with handle | Aluminium with antimicrobial epoxy-polyester powder paint finishing, white (RAL 9003/30%) | Handle aluminium profile |
20 | Filter service door | Aluminium with antimicrobial epoxy-polyester powder paint finishing, white (RAL 9003/30%) | - |
21 | Catalytic hepa filter | Catalytic absorption treated fiberglass paper, plastic frame | Filter size 300x750x48mm, ePM1 55% (Potassium permaganate) |
22 | Hepa filter | Fibreglass paper, plastic frame | Filter size 300x750x48mm, ePM1 55% |
Dimensions and weight
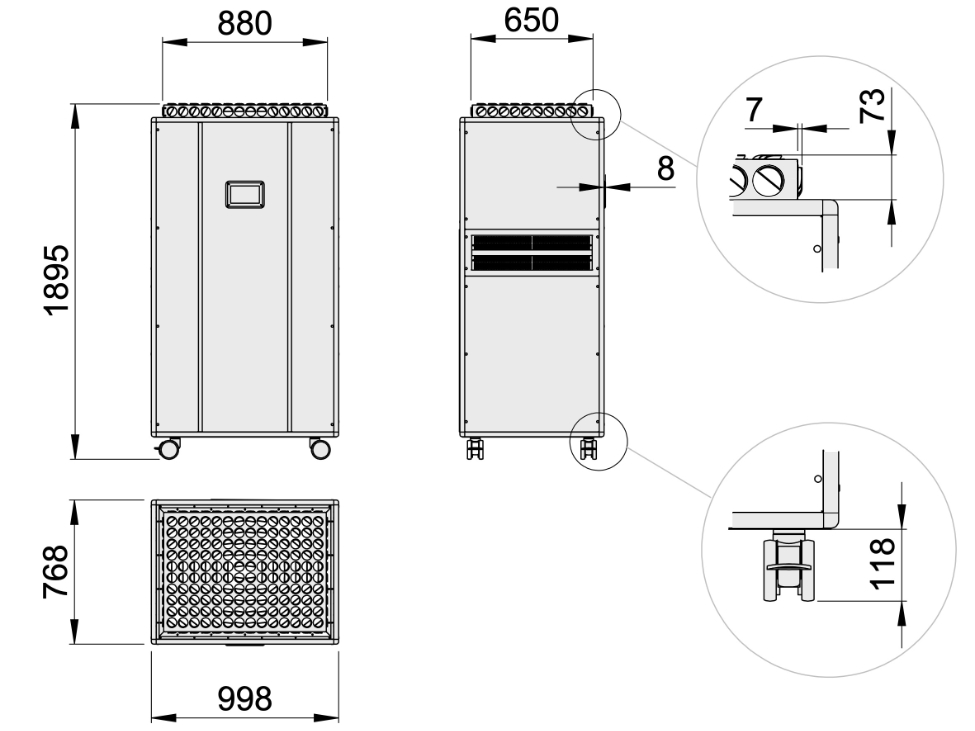
Specification
The Halton Vita VDU is a decontamination unit designed for demanding hydrogen peroxide bio-decontamination processes. It uses up to 60% aqueous hydrogen peroxide (H2O2) solution to generate hydrogen peroxide vapour capable of destroying even the most resistant microorganisms, like bacterial spores, at room temperatures and low concentrations. Halton Vita VDU decontamination units should always be used only with a compatible H2O2 liquid solution. The unit has a user interface consisting of a touch-screen monitor and a Windows CE device. In addition to this the system can have a remote user interface in a mobile device, laptop or desktop computer utilising either wireless 802.11 network or wired Ethernet.
Material
- Galvannealed steel with antimicrobial epoxy-polyester powder paint finishing for sensitive parts such as touch screens, electrical cabinets, service doors, etc.
- Aluminium with antimicrobial epoxy-polyester powder paint finishing for grills, doors and plates
-
It contains two filters: a regular filter and a catalytic filter to absorb H2O2.
-
An integrated control unit that can be connected remotely
Packaging
- The Halton Vita VDU assemblies are packed to EUR/EPAL with pallet collars or tailor-made containers for assembly transportation.
Maintenance
- Annual maintenance involves a comprehensive evaluation and servicing of equipment to ensure optimal performance and longevity. Key tasks include replacing vaporizers to maintain efficiency, calibrating pumps for precise operation, and upgrading software releases where applicable to enhance functionality and security. Additional checks and services may be conducted as needed.
- During annual maintenance, some components are either replaced or calibrated. This list does not include replacement due to damage or negligence by the user.
Service
- The Halton Vita VDU follows quality standards for the feedback process and complaint handling for any customer complaints or issues. The first point of contact for the end customer is the support organisation of the seller organisation. Halton's principle is to provide support during office hours if the customer does not have a service contract in place.
- The process of handling customer cases, claims, or issues is the same during and after the warranty period. However, the customer cases that are related to products with warranty will get priority over the non-warranty time claims. Also, customers with service contracts will have a priority.
Conformity to standards
The product adheres to the following standards and directives, ensuring compliance with EU regulations:
-
Standards:
- EN 55011:2009+A1:2010
- EN 61000-6-3:2007+A1:2011+A1:2012
- EN 61000-6-2:2005+AC:2005
- EN 301 489-1 V1.9.2
-
Directives:
- Machinery Directive (MD)
- Restriction of Hazardous Substances (ROHS)
- Radio Equipment Directive (RED)
- Waste Electrical and Electronic Equipment (WEEE)
This adherence ensure the product follows the required safety, electromagnetic compatibility, environmental, and operational standards.
Installation
The Halton Vita VDU is a large device mounted on wheels that can be moved to any location using handles. However, locking the wheels at the location avoids movement during operation.
Installing a Halton Vita VDU that uses hydrogen peroxide (H2O2) requires precise planning due to its chemical reactivity and potential safety hazards.
- Ensure the installation complies with relevant safety standards.
- Evaluate environmental controls that affect hydrogen peroxide effectiveness.
-
Check H2O2 reservoir for appropriate levels
- Room sealing is vital to prevent vapour leakage during operation.
- Ensure adequate drainage for condensate, if any.
- Ensure the spill kits and neutralizing agents are available and nearby.
- Ensure the presence of H2O2 personal protective equipment.
- Use only compatible H2O2 grade (PT02, PT04).
- Install additional sensors for monitoring H2O2 concentration.
- Connect the device to the power supply, typically 16 amp.
Place the device at the desired location to ensure proper coverage. Check that it is accessible for maintenance and operation needs. Ensure that the control panel attached to the device is working as intended and all controls are working, e.g., target concentration, time required for ramp-down, etc.
Commissioning
Ensure that the unit operates as intended, meets safety standards, and effectively achieves the desired level of decontamination.
- Make sure to complete all installation steps.
- Ensure compliance with defined regulatory and quality standards.
- Check that all components are installed correctly without any damage.
- Confirm that the device is connected and operational without any errors or malfunctions.
- Place chemical indicator (tape that changes colours over 300 ppm of H2O2) in hard-to-reach areas to confirm H2O2 reach visually.
- Monitor H2O2 levels after the cycle to ensure re-entry.
- Ensure desired decontamination levels are reached.
Maintenance
Annual maintenance of Halton Vita VDU involves a comprehensive evaluation and servicing of equipment to ensure optimal performance and longevity. Key tasks include replacing vaporisers to maintain efficiency, calibrating pumps for precise operation, and upgrading software releases where applicable to enhance functionality and security. Additional checks and services may be conducted as needed, addressing any specific issues or requirements unique to the equipment to ensure seamless and reliable performance throughout the year.
During annual maintenance, some components are either replaced or calibrated. This list does not include replacement due to damage or negligence by the user.
Components | Maintenance | Description |
---|---|---|
Evaporator cells | Replacement | Each Halton Vita VDU unit contains five evaporator cells in one mount. All cells are replaced during annual maintenance. |
CAT Filters | Replacement | Each Halton Vita VDU unit contains two CAT filters, one on each side. Both CAT filters are replaced during annual maintenance. |
Liquid hoses | Replacement | All liquid hoses should be replaced during the maintenance of evaporator cells. |
Vaisala HPP272 Sensor | Calibration | Halton Vita VDU contains one Vaisala HPP272 sensor built into the unit. This sensor is calibrated/changed annually during the maintenance of the Halton Vita VDU unit. |
LC sensor | Calibration | Optionally Halton Vita VDU may include either integrated or external low-concentratio vH2O2 concentration sensor (e.g. Dräger x-AM 5100). Also, these low-concentration sensors need to be calibrated according to manufacturer instructions. In the case of Dräger x-AM 5100, the calibration interval is 12 months. |
Order code
VDU-U-M; CO-ZT
Main options | |
---|---|
U = Unit performance | 750 |
M = Model | |
N | Nozzle outlet |
D | Ducted outlet and inlet |
Other options and accessories | |
---|---|
CO = Colour | |
HA | Signal white + (antibacterial, RAL 9003) + blue (RGB 36-157-213) |
X | pecial colour (RAL xxxx) |
ZT = Tailored product | |
N | No |
Y | Yes (ETO) |
Order code example |
---|
VDU-750-N; CO=HA, ZT=N |
Downloads
"*" indicates required fields